What is Lean?
Unlock the power of Lean principles! Discover efficiency redefined with key concepts and benefits explained concisely.
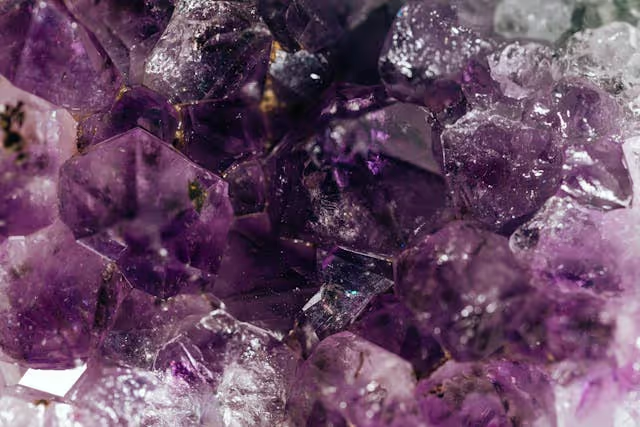
The Foundation of Lean
Understanding the essence of lean methodology is fundamental to enhancing operational efficiency and performance. By exploring the origin and fundamentals of lean principles along with key concepts in lean methodology, organizations can embark on a journey towards process optimization and waste reduction.
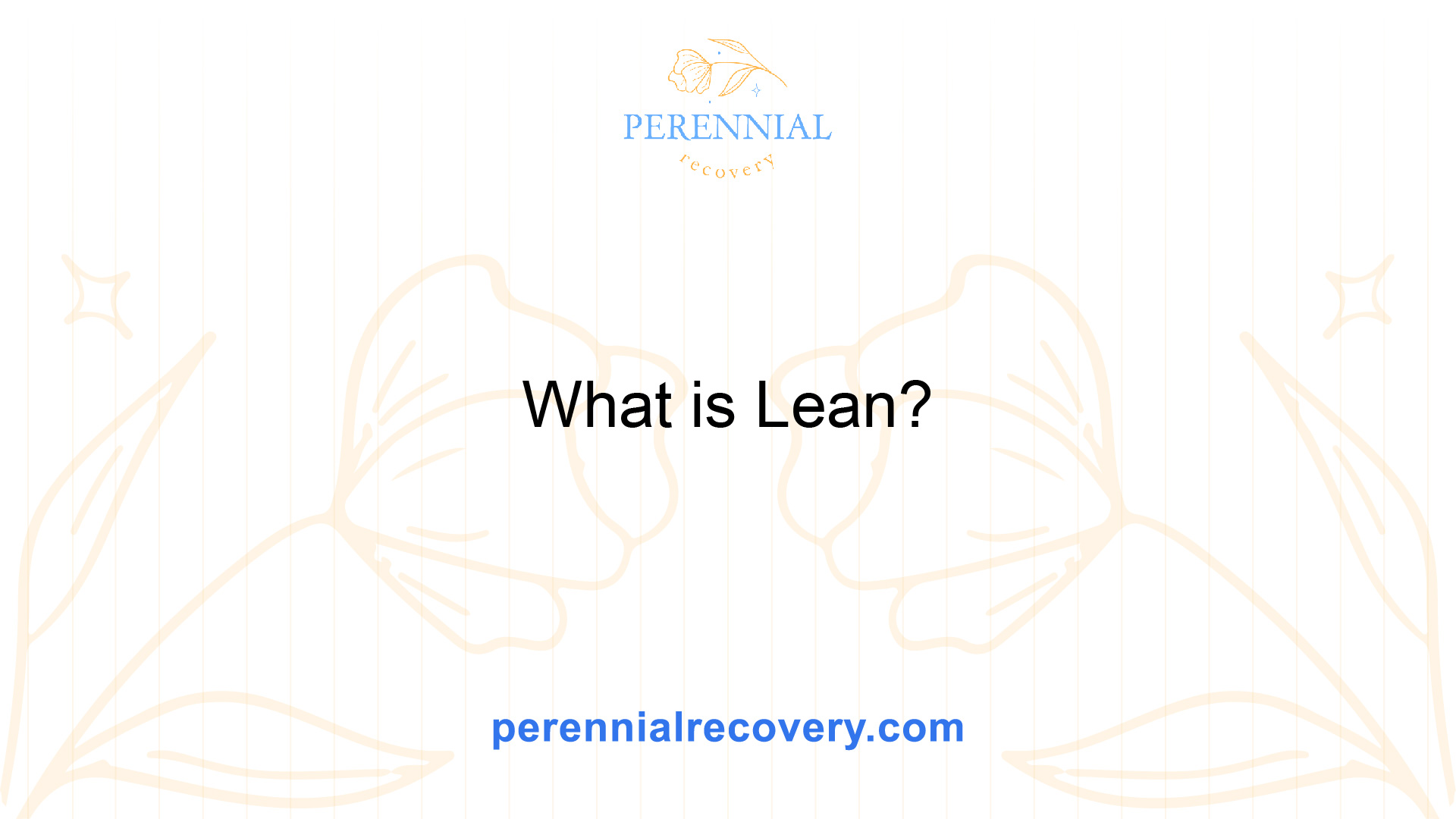
Origin and Basics of Lean Principles
The roots of lean principles can be traced back to the renowned Toyota Production System (TPS), developed by Toyota in the mid-20th century. The core idea behind lean is to maximize customer value while minimizing waste through continuous improvement efforts. Lean principles emphasize the elimination of non-value-adding activities and the creation of streamlined processes to deliver high-quality products and services efficiently.
Key Concepts in Lean Methodology
Key concepts in lean methodology revolve around:
- Value: Identifying customer value and aligning processes to deliver that value.
- Value Stream Mapping: Visualizing processes to understand flow and identify areas for improvement.
- Waste Elimination: Eliminating activities that do not contribute to value creation, such as overproduction, waiting times, and excess inventory.
In the context of lean methodology, the focus is on creating a culture of continuous improvement and empowerment where every employee is encouraged to contribute towards enhancing efficiency and reducing waste. By embracing lean principles, organizations can strive for operational excellence and sustainable growth.
By laying a strong foundation in the origin and basics of lean principles, businesses can pave the way for successful implementation and integration of lean thinking into their processes, driving transformative results and fostering a culture of continuous improvement.
Principles of Lean Thinking
In the realm of lean methodology, there are fundamental principles that guide the implementation of efficient and effective processes. Three key principles of lean thinking are value identification and streamlining, value stream mapping, and eliminating waste. Let's delve into each of these principles to understand their significance in enhancing operational efficiency.
Value Identification and Streamlining
One of the core tenets of lean thinking is to focus on value from the customer's perspective. This principle emphasizes the identification of activities within a process that directly contribute to meeting customer needs and preferences. By recognizing value-adding activities and eliminating non-value-adding tasks, organizations can streamline their operations and enhance overall efficiency.
Value identification involves understanding what customers are willing to pay for and aligning operational efforts towards delivering those specific requirements. By eliminating activities that do not contribute to the final product or service, organizations can optimize their processes and enhance value creation.
Value Stream Mapping
Value stream mapping is a visual tool used in lean methodology to analyze and optimize the flow of materials and information within a process. This technique allows organizations to identify inefficiencies, bottlenecks, and waste in their workflow by mapping out every step from the beginning to the end of a process.
By creating a value stream map, organizations can gain a holistic view of their current processes and identify areas for improvement. This data-driven approach enables teams to make informed decisions about streamlining operations, reducing cycle times, and enhancing overall productivity.
Eliminating Waste
Waste elimination is a critical aspect of lean thinking that aims to minimize activities and resources that do not add value to the final product or service. In lean methodology, waste is broadly categorized into seven types: overproduction, waiting, transport, overprocessing, inventory, motion, and defects. By identifying and eliminating these sources of waste, organizations can optimize their processes and reduce inefficiencies.
By focusing on eliminating waste, organizations can increase the value delivered to customers, reduce costs, and improve overall operational performance. Lean practitioners often employ tools and techniques such as 5S, standard work procedures, and continuous improvement to systematically identify and eliminate waste in their operations.
Understanding and applying the principles of value identification and streamlining, value stream mapping, and waste elimination are essential for organizations looking to embrace lean thinking and drive continuous improvement in their operations. By adopting these principles, organizations can enhance efficiency, reduce costs, and deliver greater value to their customers.
Core Elements of Lean Implementation
When it comes to implementing Lean principles, there are essential core elements that form the foundation of this methodology. These core elements focus on driving continuous improvement, optimizing production processes, and emphasizing the value of individuals within the organization. Let's delve into three key components of Lean implementation: Continuous Improvement (Kaizen), Just-in-Time Production, and Respect for People.
Continuous Improvement (Kaizen)
Continuous Improvement, often referred to as Kaizen, is a fundamental principle in Lean methodology. It emphasizes the ongoing efforts to enhance processes, products, and services incrementally. Kaizen encourages all employees, from the frontline workers to top management, to actively participate in identifying opportunities for improvement and implementing changes.
The key aspect of Kaizen is the philosophy of making small, continuous changes rather than large, disruptive transformations. By fostering a culture of continuous improvement, organizations can streamline operations, boost efficiency, and adapt quickly to changing market demands. Kaizen promotes the idea that improvement is a never-ending journey, and every improvement, no matter how small, contributes to the overall success of the organization.
Just-in-Time Production
Just-in-Time (JIT) Production is another critical element of Lean implementation that aims to reduce waste and improve efficiency in production processes. The JIT approach entails producing goods or services precisely when they are needed, in the required quantities, and at the right quality. By aligning production closely with customer demand, organizations can minimize inventory holding costs, reduce lead times, and enhance overall responsiveness.
One of the primary benefits of JIT production is its ability to identify and eliminate inefficiencies in the production process. By synchronizing production with customer demand, organizations can avoid overproduction, excess inventory, and unnecessary waiting times. JIT production also helps enhance quality control by detecting and addressing defects early in the production cycle, leading to higher customer satisfaction and lower costs.
Respect for People
Respect for People is a core value in Lean methodology that emphasizes the importance of valuing and empowering employees at all levels of the organization. This principle acknowledges that employees are the most valuable asset and advocates for creating a work environment where individuals feel respected, engaged, and motivated to contribute their best efforts.
By fostering a culture of respect for people, organizations can nurture creativity, collaboration, and innovation among employees. Empowering employees to make decisions, voice their opinions, and take ownership of their work leads to higher job satisfaction, increased morale, and improved overall performance. Respect for People not only enhances employee engagement but also drives organizational success by harnessing the collective talent and expertise within the workforce.
Incorporating these core elements of Lean implementation—Continuous Improvement (Kaizen), Just-in-Time Production, and Respect for People—can help organizations achieve operational excellence, drive innovation, and create a culture of continuous learning and improvement. By embracing these principles, organizations can optimize their processes, enhance employee engagement, and deliver exceptional value to their customers.
Lean Management Techniques
In the realm of lean practices, various management techniques play a crucial role in optimizing processes and maximizing efficiency. Three fundamental lean management techniques include standardized work, the 5S system, and visual management.
Standardized Work
Standardized work is a cornerstone of lean methodology, emphasizing the importance of documenting and following standardized procedures for each task within an organization. By establishing clear and consistent work instructions, organizations can eliminate variability, improve quality, and enhance employee productivity.
This approach involves breaking down tasks into detailed steps, setting specific work sequences, and defining quality standards. Standardized work not only streamlines operations but also enables continuous improvement through the identification of inefficiencies and opportunities for enhancement.
5S System
The 5S system is a methodology aimed at organizing the workplace for efficiency and effectiveness. The 5S principles—Sort, Set in order, Shine, Standardize, and Sustain—guide organizations in creating a clean, organized, and visually controlled work environment.
By implementing the 5S system, organizations can eliminate clutter, reduce unnecessary movement, and improve overall workflow efficiency. Each 'S' represents a specific action to be taken in order to optimize the workspace and create a more productive and safe working environment.
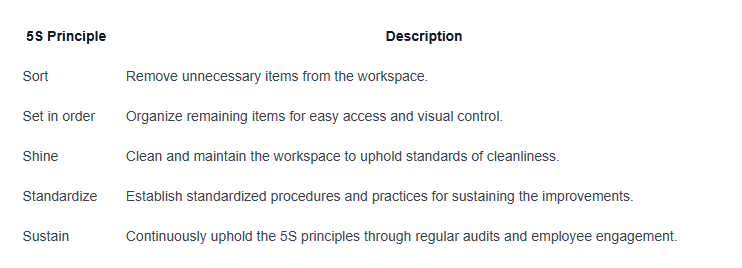
Visual Management
Visual management is a lean technique that utilizes visual cues and signals to communicate information, status, and performance metrics in the workplace. By incorporating visual tools such as signs, charts, and displays, organizations can enhance communication, transparency, and decision-making processes.
Visual management enables employees to quickly grasp key information, identify abnormalities, and monitor progress in real-time. Visual displays, such as Kanban boards and performance dashboards, help teams track workflow, prioritize tasks, and address issues promptly. This visual approach fosters a culture of accountability, continuous improvement, and operational excellence.
By incorporating standardized work, the 5S system, and visual management into their operational processes, organizations can streamline workflows, enhance workplace organization, and drive sustained improvements in performance and efficiency within the lean framework.
Tools and Methodologies in Lean
Exploring the tools and methodologies within the realm of lean methodology reveals a range of techniques designed to enhance efficiency and streamline processes. Three key tools in lean methodology are the Kanban system, Poka-Yoke (Error Proofing), and Root Cause Analysis.
Kanban System
The Kanban system is a visual management tool that originated from lean manufacturing practices. It involves the use of signals or cards to represent the status of tasks or items in a workflow. By visually displaying the progress of work and limiting work in progress, the Kanban system helps teams prioritize tasks, identify bottlenecks, and maintain a smooth flow of work.
The Kanban system typically consists of three main columns: "To-Do," "In Progress," and "Done." This visual representation allows team members to quickly grasp the status of each task and make informed decisions on task allocation and resource management.
Poka-Yoke (Error Proofing)
Poka-Yoke, also known as error proofing, is a lean technique focused on preventing errors or defects during the production process. The goal of Poka-Yoke is to design processes in a way that makes it impossible for mistakes to occur or easily detect and correct errors before they result in defects.
This methodology relies on the use of mechanisms such as sensors, alarms, and physical barriers to prompt operators to take corrective actions when deviations from standard procedures are detected. By integrating Poka-Yoke into workflows, organizations can improve quality, reduce rework and scrap, and enhance overall process reliability.
Root Cause Analysis
Root cause analysis is a structured method used in lean management to identify the underlying reasons for problems or defects within a process. By digging deep into the root causes of issues rather than addressing symptoms, organizations can implement effective solutions that prevent recurrence and drive continuous improvement.
Root cause analysis typically involves techniques like the "5 Whys," where the team iteratively asks "why" a problem occurred to uncover successive layers of causation until the fundamental issue is revealed. This method enables organizations to address the core issues that hinder efficiency and quality, leading to sustainable improvements in processes and outcomes.
These tools and methodologies play a significant role in the successful implementation of lean principles, enabling organizations to optimize operations, enhance quality, and drive continuous improvement. By incorporating the Kanban system, Poka-Yoke, and Root Cause Analysis into their workflows, companies can achieve greater efficiency, productivity, and reliability across diverse industries.
Lean in Different Industries
When it comes to implementing lean principles, the methodology transcends various industries, adapting its core concepts to suit the specific needs and challenges of different sectors. Two prominent sectors where lean practices have made a significant impact are manufacturing and the service and healthcare industries.
Lean in Manufacturing
In the realm of manufacturing, lean principles have revolutionized traditional production processes, emphasizing efficiency, waste reduction, and continuous improvement. By streamlining production flows and optimizing resource utilization, manufacturers can enhance productivity, reduce costs, and deliver higher quality products to their customers.
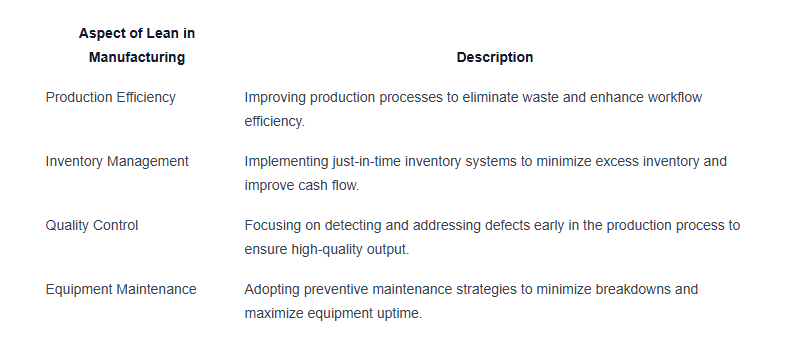
Lean in Service and Healthcare Industries
In the service and healthcare industries, lean methodologies have reshaped service delivery, patient care, and operational efficiency. By applying lean principles such as value stream mapping, continuous improvement, and standardized work practices, organizations in these sectors can streamline operations, enhance customer satisfaction, and optimize resource allocation.
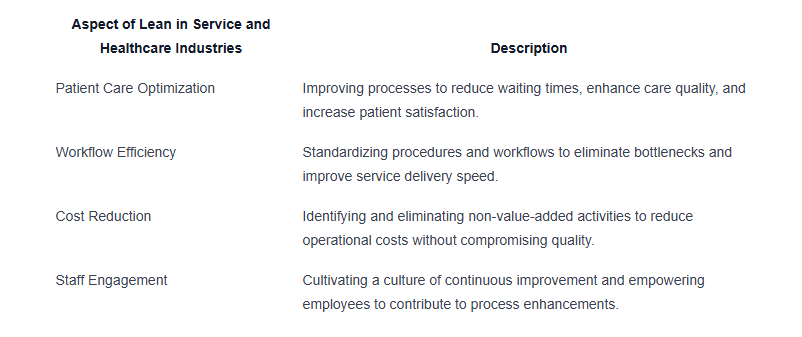
By embracing lean principles in manufacturing, service, and healthcare industries, organizations can drive operational excellence, foster a culture of continuous improvement, and ultimately deliver greater value to their stakeholders. The adaptability of lean methodologies allows businesses in diverse sectors to reap the benefits of efficiency, quality enhancement, and sustainable growth.
Benefits of Lean Thinking
Embracing Lean principles in an organization can lead to a multitude of advantages, ultimately driving operational excellence and fostering continuous improvement. Let's delve into the key benefits that Lean thinking can bring to businesses across various industries.
Efficiency and Productivity Improvements
One of the primary benefits of Lean methodology is the significant enhancement in efficiency and productivity. By identifying and eliminating non-value-added activities and streamlining processes, organizations can optimize their operations to achieve higher output with minimal resources.
Table: Efficiency and Productivity Improvements
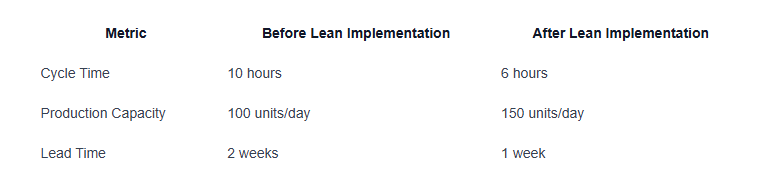
Cost Reduction and Waste Minimization
Implementing Lean practices enables organizations to cut costs and reduce waste significantly. By focusing on value-adding activities and eliminating inefficiencies, companies can streamline operations and allocate resources more effectively, leading to cost savings and improved profitability.
Table: Cost Reduction and Waste Minimization
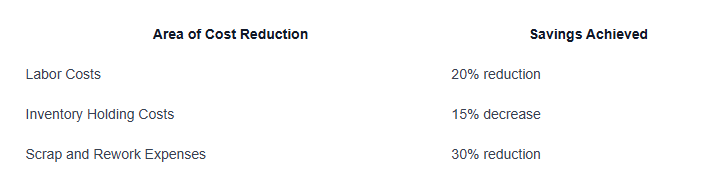
Enhanced Quality and Customer Satisfaction
Lean thinking emphasizes the importance of continuous quality improvement and customer-centricity. By fostering a culture of quality and implementing measures to prevent defects, organizations can enhance the quality of their products or services. This, in turn, leads to increased customer satisfaction and loyalty.
Table: Enhanced Quality and Customer Satisfaction

These key benefits highlight the transformative impact that Lean thinking can have on organizations, paving the way for sustainable growth, competitiveness, and customer-centric service delivery.
Challenges and Considerations in Implementing Lean
Implementing lean methodologies in an organization comes with its own set of challenges and considerations that need to be addressed to ensure successful implementation and sustainability. Three key aspects that organizations often encounter are cultural shift and employee resistance, sustaining lean practices, and alignment with organizational goals.
Cultural Shift and Employee Resistance
One of the primary challenges in implementing lean practices is the need for a cultural shift within the organization. Lean principles require a mindset focused on continuous improvement, waste reduction, and efficiency, which may conflict with the existing organizational culture. Resistance from employees who are used to traditional work processes can hinder the adoption of lean practices.
To overcome this challenge, organizations should invest in comprehensive training programs to educate employees about the benefits of lean and involve them in the implementation process. Creating a culture of open communication, collaboration, and empowerment can help mitigate resistance and foster acceptance of lean methodologies.
Sustaining Lean Practices
Another significant consideration in lean implementation is the sustainability of lean practices over time. While initial improvements may be achieved through the implementation of lean methodologies, maintaining these practices and ensuring continuous improvement can be a demanding task. Without ongoing commitment and dedication from all levels of the organization, the gains achieved through lean practices may diminish.
To sustain lean practices, organizations should establish mechanisms for monitoring and evaluating performance, conducting regular audits to identify areas for improvement, and providing ongoing training and support to employees. Creating a culture of accountability and continuous learning can help embed lean principles into the organizational framework and ensure long-term success.
Alignment with Organizational Goals
For lean implementation to be effective, it is essential to align lean practices with the broader strategic goals and objectives of the organization. Without clear alignment with the organizational vision, mission, and values, lean initiatives may lack direction and fail to deliver meaningful outcomes. It is crucial for organizations to integrate lean principles into their overall strategic planning processes and ensure that lean practices support and complement the organizational goals.
By aligning lean methodologies with organizational goals, organizations can enhance the relevance and impact of lean practices, driving sustainable improvements in efficiency, productivity, and quality. Regularly assessing the alignment between lean initiatives and organizational objectives can help organizations make necessary adjustments and maximize the benefits of lean thinking across all levels of the organization.
Sources
https://www.addictioncenter.com/opiates/codeine/lean-addiction-abuse/
https://www.cwcrecovery.com/blog/what-is-lean-understanding-lean-addiction-and-abuse/
https://www.sciencedirect.com/science/article/abs/pii/S0306460313000920
Learn More
Read the latest addiction news and recovery tips from our blog.
Perennial Recovery Privacy Policy
Perennial Recovery Electronic Signature and Records Terms and Conditions